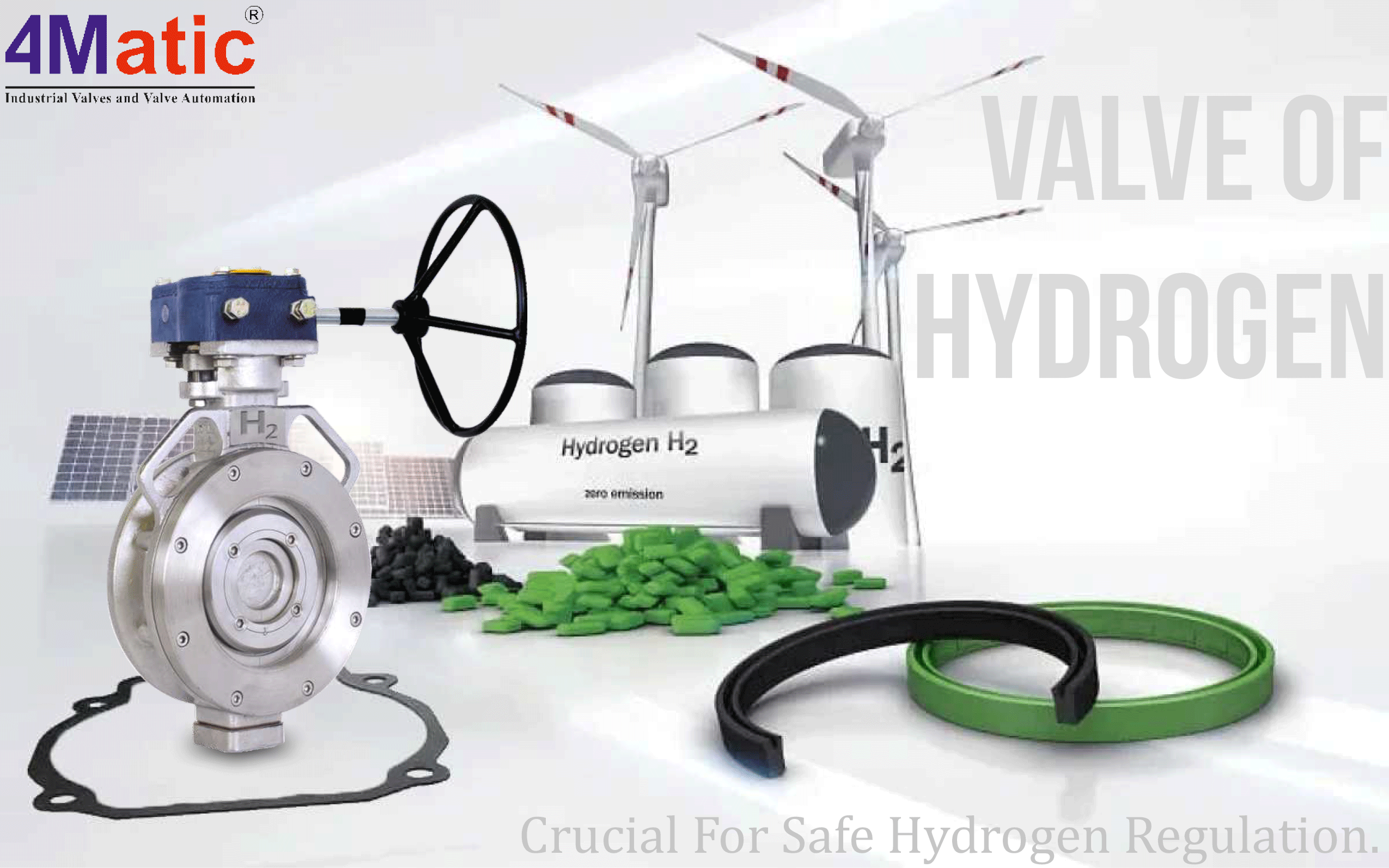
The hydrogen industry has received a remarkable concentration in the present-day industrial scenario due to the acute need of clean energy sources. As there is a constant increase in the demand of hydrogen, it becomes vital to pay attention to the likely safety measures linked to the industrial valves utilized in hydrogen service. In this fast-developing industry, actions pertaining to safeguarding need, and crucial attentiveness, like, material choosing, design verification testing, fugitive emission trial etc. Affirmation of their functionalism by design verification testing for industrial valves in hydrogen service is very important to rest assured that they are dependable in asking operating situations also.
Hydrogen is the most tiny molecule but has enormous probalities as an energy originator. Hydrogen valves have a key role, as they regulate the flow of this extremely flammable gas so as to ensure the safeguarding of personnel, equipment as well as the environment.
Choice of Valve
As for hydrogen service applications, it is of utmost importance to select the proper valve, as far as safety and reliability are concerned. Usually, the valve types that are made use of for hydrogen service include ball valves, globe valves, and check valves. For on/off service as well as for shut-off competence, Ball valves are considered perfectly outstanding and hence they become most viable for hydrogen isolation applications.
Due to their perfect flow control and throttling abilities, globe valves are time and again used in hydrogen systems where flow control is mandatory. Check valves are most useful in keeping up the integrity of hydrogen systems by averting backflow and for system safeguarding. Compliance with industry norms, like API 600, API 602, and ASME B16.34 is necessary while choosing valve types for hydrogen service so as to have compatibility and accomplishment.
SOURCE MATERIALS
For the purpose of safety and reliability, the selection of the correct materials for valves in hydrogen service is very important. For hydrogen service, usually prescribed materials are inclusive of stainless steel (ASTM A351 CF8M), nickel-based alloys (ASTM B564, N10276), and titanium (ASTM B348). These materials show high defiance to hydrogen embrittlement and are fit for the purpose of resisting the peculiar challenges raised by hydrogen service conditions.
ASTM International, the American Petroleum Institute (API), and the American Society of Mechanical Engineers (ASME) are the organizations, that issue worthwhile recommendations for the choice of material and compatibility in hydrogen service.
VERIFICATION OF DESIGN & TESTING
Hydrogen valves are designed to resist the peculiar challenges linked with operating this volatile gas and therefore safety is of utmost importance. These valves must show the capacity to control high pressure, avert leakages and keep up systematic flow control to minimize the hazards related to hydrogen, the safety of both human lives and precious assets.
Verification of their workability through design validation testing for industrial valves in hydrogen service is very important to be rest assured that they are dependable under challenging functioning conditions. The types of tests prescribed for verification of design are inclusive of engineering design calculations and simulations, pressure testing to evaluate structural uprightness and leak proofness at high pressures, and cycling of the valves in simulation-type testing situations. It is advised to have automation while cycling so as to safeguard the personnel.
There is an increasing drift in pneumatic testing in comparison to hydrostatic testing for valves because of the chances for water to obstruct very small, microscopic faults at lower pressure testing or because of water contamination within particular valve designs. The use of an inert gas alternative may give a higher level of sensitivity in testing. Functional testing in the same operational conditions through the use of media, for instance, clean dry air, nitrogen, helium, argon or may be hydrogen itself must be undertaken by professionals who are skillful in handling these peculiar threats.
As far as higher-pressure pneumatic testing is concerned, the use of bunkers is fairly considerable. It is necessary to have cryogenic testing for validating the functionality of valves at low temperatures, specifically for hydrogen service. It is important to have conformity of valve design and testing with industrial norms like API 598 and ASME B16.34 but to comply with added assurance relying on service conditions, it is usually observed that extra testing times and methods beyond normal limits are also furnished.
FUGITIVE EMISSIONS
While choosing a valve for hydrogen service, the primary considerations i.e., functional testing, pneumatic testing and cryogenic testing are not enough. The valves should be made subject to fugitive emissions and fire testing so as to have an assurance that they are competent to face any negative eventuality.
Is it cost effective to combine functional testing and emission testing? An operating valve, under the most demanding circumstances can decrease emissions, pollution and thus works as a silent safeguard of lives. As far as fugitive emissions testing for industrial valves in hydrogen service, is concerned it is advisable to go for the précised testing methods, so as to be assured with regard to environmental and operational safety. Helium leak testing with the use of mass spectrometry or gas detection techniques is generally utilized for evaluating the leakage rates of valve which have unusual sensitivity.
Usually, this testing procedure is used in processes based on ASME V methods. These methods enable for the spotting of very small leaks which may not be recorded on a normal analog gauge, verifying that valves are strictly in accordance to the emission norms and marginalize the danger of fugitive emissions.
To add to this, compliance with fugitive emission standards i.e., ISO 15848-1 and API 622/624 is necessary to attend to the environmental influence and anxieties regarding safety linked with hydrogen service.
FINALLY….
In the hydrogen industrial valves industry, safety requires very careful attention as far as choosing the material, design verification testing, right type of valve, testing of fugitive emissions and careful thought on the confrontations posed by hydrogen service based on risk portrayal. Through prior focusing on these issues and linking them with industry norms and best practices, manufacturers and industry collaborators can endorse the top most safety norms and contribute to the dependable as well as durable usage of hydrogen as an energy initiator. Along with the advancement in hydrogen industry it is equally important to have sincere commitment with regard to safety norms so as to succeed in this sector together with building public confidence in this transformative energy field.
For More Information Contact here.
www.4maticvalves.com / info@4maticvalves.com