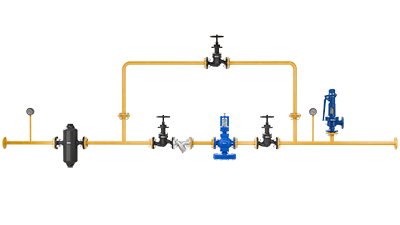
Equipment Protection: Many steam-operated devices and equipment are designed to operate within specific pressure ranges. Exposing them to excessive pressure can lead to damage or malfunction. By reducing the pressure to an appropriate level, the pressure reducing station helps protect these devices.
Energy Efficiency: Operating steam systems at unnecessarily high pressures can result in energy waste. By reducing steam pressure to the minimum required for the application, the pressure reducing station contributes to energy efficiency and cost savings.
Process Control: Certain industrial processes require steam at precise pressures to maintain optimal conditions. Pressure reducing stations enable precise control over steam pressure, ensuring consistency and quality in these processes.
Distribution: In large steam distribution systems, steam may be generated at high pressures and then distributed to various users at lower pressures. Pressure reducing stations are used at strategic points along the distribution network to regulate pressure as needed for different users or sections of the system.
- What is boiler output flow rate?
- Required Maximum flow rate?
- What is maximum inlet pressure?
- What is the pressure or flow rate turndown ratio of steam?
- What is the steam type: dry saturated/wet steam/superheated?
- What is the required total length of the Steam PRS?
- For what application will the steam PRS be installed?
- How stringent are the steam quality requirements?
- Are there any site specific loads for the installed pressure reducing station? Like seismic zone, wind loads etc.?
- What is the ambient temperature for the steam pressure reducing station?
- What is the maximum safety set pressure of the steam?
- Does the steam require superheating?
- How much optimum is the condensate recovery management system of the process plant?
Steam PRS with Pilot operated, self-acting Pressure Reducing Valve
Description
These employ a sophisticated self-acting design, functioning by sensing downstream pressure through a pilot valve, which subsequently operates the main valve. This setup yields an exceptionally narrow proportional band, typically less than 200 kPa. Combined with minimal hysteresis, this design ensures precise and repeatable pressure control, even amidst fluctuating flow rates.
Advantages:
- Ensures accurate and consistent pressure control, even with varying and high flow rates.
- Offers versatility with multiple pilot valve options for a single main valve, including electrical override, multi-pilot for diverse control pressures, surplus control, remote control, and various temperature/pressure control combinations.
- Self-acting operation eliminates the need for external power.
- Exhibits tolerance to varying upstream pressure.
Disadvantages:
- Higher cost compared to bellows-operated direct acting controls.
- Requires clean and dry steam due to small clearances, but this can be managed with a strainer and separator before the pressure reducing valve.
Application:
- Ideal for systems demanding precise and consistent pressure control, particularly those with variable and medium flow rates, such as autoclaves, high-rated heat exchangers, and calorifiers.
- Suitable for installations with limited space.
Points to note:
Installation must include a strainer and separator.
- Installation necessitates a strainer and separator.
- While more expensive than bellows-type self-acting controls, they are less costly than diaphragm-type controls.
- Offers higher capacity than bellows-type controls but less than diaphragm-type.
- Can be installed upstream of temperature control valves to maintain constant upstream pressure.
- Not suitable for liquid applications or environments prone to vibration or flow pulsations.
Pressure reduction – electropneumatic
Description
These control systems may include:
Our cutting-edge control systems are equipped with P + I + D functions to ensure accuracy, even amidst varying load conditions. They offer the convenience of remotely adjusting set points, with the added feature of smooth ramps between them.
Advantages:
- Flexibility and precision are unmatched.
- Remote adjustability and monitoring enhance convenience.
- Valve size is unrestricted within defined limits.
- Achieves up to 50:1 flow rangeability, typically seen in globe control valves.
- Rapid response to demand fluctuations.
- Handles high differential pressures across valves with ease.
Disadvantages:
- More expensive than self-acting or pneumatic controls.
- More complex than self-acting or pneumatic controls.
- Electrical control signal required. Costly for hazardous areas.
Application:
Tailored for systems requiring precise and consistent pressure control, particularly those with variable and high flow rates or fluctuating upstream pressures. Applications include autoclaves, large heat exchangers, calorifiers, and main plant pressure reducing stations.
Points to note:
- A clean, dry air supply is required.
- A skilled workforce is required to install the equipment, and instrument personnel are required for calibration and commissioning.
- Can be part of a sophisticated control system involving PLCs, chart recorders and SCADA systems.
- Always consider the failure mode, for example, spring-to-close on air failure is normal on steam systems.
Pressure reduction – electric
Description
These control systems may include:
- P + I + D functions to improve accuracy under varying load conditions.
- Set point(s), which may be remotely adjusted.
Advantages:
- Both the controller and valve actuator possess the capability to interface with a PLC.
- Eliminates the need for a compressed air supply.
Disadvantages:
- The utilization of a spring return actuator might impose limitations on available shut-off pressure. • Actuator speed is relatively sluggish, rendering it suitable only for applications characterized by gradual load changes.
Application:
- Applicable to slow opening or warm-up systems featuring a ramp and dwell controller. • Ideal for pressure control in large-scale autoclaves. • Suited for pressure reduction in supplying extensive steam distribution systems.
Points to note:
- Safety: If electrical power is lost the valve position cannot change unless a spring return actuator is used.
- Spring return actuators are expensive and bulky, with limited shut-off capability.
Pressure reduction (other possibilities) – Parallel pressure reducing stations
Description
Pressure reducing stations can be arranged in the following manner for one of two purposes:
- In situations where the valves are serving critical applications where downtime is unacceptable, a ‘one in operation, one on stand-by’ approach is adopted. This ensures continuous operation by having equipment operating alternately to cover for breakdowns and maintenance.
- Alternatively, if there is a significant turndown ratio between maximum and minimum flow rates, the equipment is operated on a pressure sequence principle. Here, one valve is set at the ideal downstream pressure, while the other is set slightly lower. When demand is high, both valves operate; as flow decreases, the valve set at the lower pressure closes first, leaving the second valve to regulate.
Important considerations: Valves chosen for such applications must have narrow proportional bands (e.g., pilot-operated pressure reducing valves or electro pneumatic control systems) to prevent excessive downstream pressure drop at high flow rates.
Pressure reduction (other possibilities) – Series pressure reducing stations
In such scenarios, a pressure reducing station can be configured to manage situations where the ratio between upstream and downstream pressure is significantly high, especially when the selected control systems have limited turndown capability. Typically, a practical maximum pressure ratio of 10:1 is recommended for this type of reducing valve.
For instance, let’s consider the requirement to reduce pressure from 25 bar g to 1 bar g. Initially, the primary reducing valve may decrease the pressure from 25 bar g to 5 bar g, representing a pressure ratio of 5:1. Subsequently, the secondary reducing valve would further reduce the pressure from 5 bar g to 1 bar g, also at a 5:1 ratio. When both valves are arranged in series, they provide a combined pressure ratio of 25:1.
It’s crucial to verify the allowable pressure turndown ratio specified for the chosen reducing valve. While a self-acting valve might have a turndown ratio of 10:1, electrically or pneumatically operated valves can offer much higher turndown ratios. Additionally, it’s essential to be mindful that significant pressure drops might lead to elevated noise levels.
Regarding the configuration, a trapping point between the two reducing valves (as illustrated in Figure 8.1.8) serves to prevent the accumulation of condensate under no-load conditions. Without this trapping point, radiation losses could cause condensate to accumulate in the connecting pipe, potentially leading to water hammer when the load increases again. For further details, Module 6.4 provides comprehensive information on this aspect.
Desuperheaters
Desuperheating is the process by which superheated steam is either restored to its saturated state, or its superheated temperature is reduced. Further coverage of desuperheaters is given in Block 15.
The system in Figure 8.1.9 illustrates an arrangement of a pressure reducing station with a direct contact type pipeline desuperheater.
In its basic form, good quality water (typically condensate) is directed into the superheated steam flow, removing heat from the steam, causing a drop in the steam temperature.
t is impractical to reduce the steam temperature to its saturated value, as the control system is unable to differentiate between saturated steam and wet steam at the same temperature.
Because of this, the temperature is always controlled at a value higher than the relevant saturation temperature, usually at 5°C to 10°C above saturation.
For most applications, the basic system as shown in Figure 8.1.9 will work well. As the downstream pressure is maintained at a constant value by the pressure control loop, the set value on the temperature controller does not need to vary; it simply needs to be set at a temperature slightly above the corresponding saturation temperature.
However, sometimes a more complex control system is required, and is shown in Figure 8.1.10. Should there be a transient change in the superheated steam supply pressure, or a change in the water supply temperature, the required water/steam flow ratio will also need to change.
A change in the water/steam flow ratio will also be required if the downstream pressure changes, as is sometimes the case with certain industrial processes.
Flow rate and Pressure drop evaluations
- Inlet and outlet pipe sizing
- Isolation valve sizing
- Application Specific pressure reducing valve selection
- Selection of Appropriate Steam Separator with Steam trap module (if required)
- Sizing Pressure reducing valve
- Sizing safety valve
- Appropriate pipe ancillaries.
Structural integrity evaluations
- Evaluating bending and shear stresses for all the pipelines complying with B31.1
- Evaluating thermal stresses and thermal expansions complying with B31.1
- Support distances as per evaluated stresses
- Flanges and welding as per ASME standards
Welding | Could provide with radiography |
IBR approved | All Components and the PRS could be provided with IBR certificates |
Structural design | Designed as per ASME B31.1 or B31.3, and other piping standards |
- Most of the components are In-house manufactured
- Expert engineering team
- Quick delivery timelines
- Global supply chain