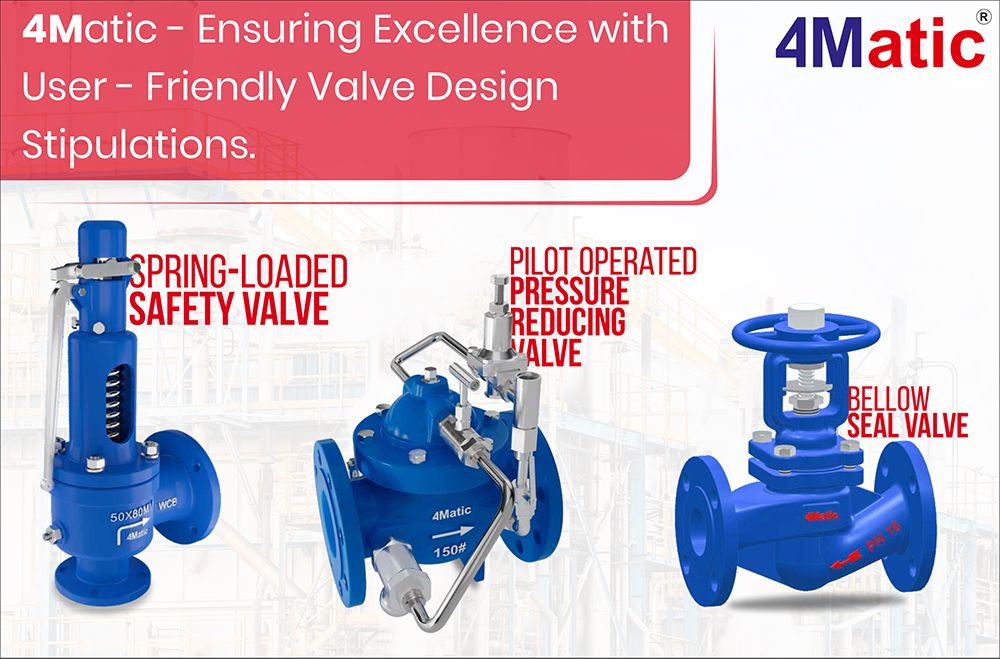
4Matic – User-Friendly Valve Design Stipulations
The end users or the actual users of valves have their own norms and prescriptions to be rest assured that their valves are in compliance with the international industry standards and raise the bar for the needed minimum of the best design against the quality of the product to have an assurance that they are all set to perform and be in running order.
Valves are crucial constituents of an operating facility where segregation is a necessity. Valves should be chosen in a precise manner with the specification with regard to the suitability of the move for the desired function and purpose. This is inclusive of adhering to the defined international norms and approved guidelines along with the development of internal codes or populations to match the organization’s administration and procedure.
Design Stipulations
Generally, large-scale energy companies have their own designed internal set of standards, course of action, and formations to serve as the lowest requirements for stipulating valves.
These codes control the stipulations or specifications which focus on several features, a few vital amongst them are as under:
– Design
– Choice of material
– Service
– Testing
– Inspection
The requisites of which of these developed codes differ as far as the service, application, and facility function are concerned. Various elements determine, case by case requirements which asses pressure, temperature, type of fluid, and other risk aspects.
Service Requisites
In general, large-scale companies have service particular instructions, which are inclusive of applications, like high temperature, sour hydrocarbons, corrosive brine products etc. In short, these requirements are inclusive of the following:
⇒ Subsea or underwater valves will be of ball design and of class 300 as lowest along with ring joint connection.
⇒ Clean dry gases may be furnished with soft seated valves, which have double block as well as bleed characteristics.
⇒ Only Gate, Ball, or Triple Offset Butterfly valves be used for Gas Flare systems.
⇒ Fire testing and design verification should be there for isolation valves.
⇒ Any drain or vent should be capped through a plug or blind.
⇒ DIB-2 seat configuration be there for Pig trap main valves and it should be only through-conduit gate or ball valves.
⇒ To add to the above, duplex stainless steel with seat pockets overlaid with Inconel 625 should be the trim material for pig trap valves.
⇒ Lubricated plug valves should be used for blowdown or kicker applications.
⇒ API 602 gate valves should be made use of as Instrument isolation valves.
The above list displays a few numbers of the many guidelines and necessities for service specifications set down as inner company norms. These being amended, modernized, and enhanced depending upon past experiences and project acquaintances to make sure that all the valves are precisely stipulated, chosen, and conceived.
Design Necessities
Furthermore, certain design necessities are stipulated to be rest assured with regard to the type of valves, design, material as well as configuration. This is inclusive of the following:
Induction of gate valves with horizontal or below orientation requires to be in clean service or utility applications to get rid of blockage of the flow line.
Seal welding is necessary for all threaded connections of valve bodies, like drains and vents.
Lever-operated valves should be furnished with self-locked handles.
Non-slam check valves should be chosen as far as rotating equipment discharge lines are concerned.
For hydrocarbon services, wafer-type check valves are not permissible.
The requirements of design are usually stipulated for each facility during the planning and also while reviewing the project, so as to be rest assured with regard to a total grasping of the process and flow framework plus further requirements, if any. Past experiences should be taken into full consideration while planning for implementing operation and maintenance exercises.
To conclude, it has been a general practice with the end users to have their specifications in a corresponding way along with the international standards set through bodies or groups like ASME, BS, API, IOGP, etc. All these come together to keep up the least required specs and are matched to rest assure the safeguarding and easy operations of the facility as well as its assets. 4Matic is committed to guaranteeing the best in hydrocarbon transportation, shipping, and handling by exercising the finest practices with an assurance of the latest specifications.
For More Information Contact Here :